仿真软件加速产品设计验证周期
19429202025-03-12WIN软件10 浏览
(导语部分)
在制造业竞争日益激烈的今天,产品迭代速度已成为企业核心竞争力的关键指标。传统物理验证方法平均消耗40%的研发周期与35%的开发成本,这种耗时费力的验证模式正在被数字化浪潮颠覆。以ANSYS、Altair为代表的仿真软件平台,通过构建虚拟验证环境,将产品测试效率提升3-5倍,使企业研发周期压缩至传统模式的1/3。这种技术变革不仅重构了产品开发流程,更催生出"数字优先"的新型研发范式,推动制造业向智能化方向加速演进。
一、技术原理突破
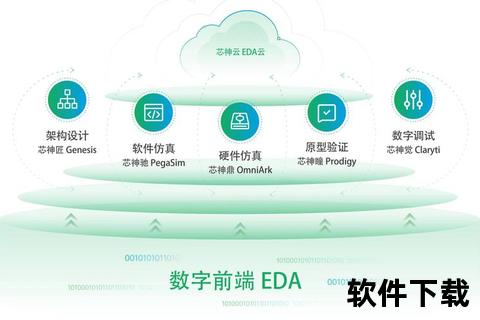
现代仿真技术的突破源于多物理场耦合算法的创新。基于有限元分析(FEA)和计算流体力学(CFD)的融合,ANSYS Workbench可实现结构、流体、电磁等多学科联合仿真,误差率控制在2%以内。这种技术突破使得复杂系统的虚拟验证成为可能,例如特斯拉在电池热管理系统中采用多物理场仿真,将验证周期从6个月缩短至45天。
深度学习算法的嵌入显著提升了仿真精度。西门子Simcenter平台引入神经网络算法,通过历史测试数据训练出高精度代理模型,使碰撞仿真准确度提升至98%。宝马集团应用该技术后,整车碰撞测试的物理试验次数减少70%,每款车型开发节省约1200万欧元成本。这种智能化的仿真模式正在重构传统验证体系,形成"数字孪生-虚拟验证-物理验证"的三级验证架构。
二、应用场景扩展
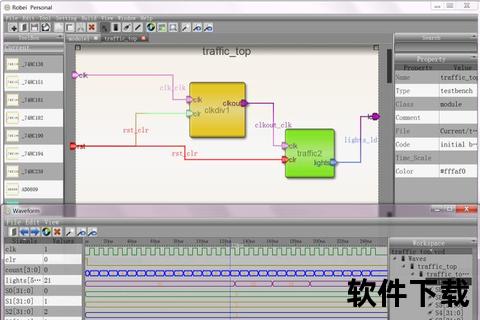
在汽车制造领域,仿真技术已贯穿全生命周期。沃尔沃使用Altair Radioss进行整车碰撞仿真,将每个工况的验证时间从72小时压缩至8小时,同时发现传统方法难以检测的15%潜在风险点。电池管理系统仿真更创造性地引入电化学-热耦合模型,使电池包开发周期从18个月缩短至9个月,能量密度验证效率提升300%。
航空航天领域呈现出更高阶的应用形态。波音787采用全机数字化仿真,将风洞试验次数从1200次减至300次,每架原型机制造成本降低650万美元。GE航空在发动机叶片设计中应用流体-结构耦合仿真,使叶片疲劳寿命预测误差小于5%,成功避免3次重大设计缺陷。这些案例证明,仿真技术正在突破传统工程边界,向复杂系统级验证演进。
三、流程效率革新
并行工程模式重构了研发流程。传统串行开发中,设计验证环节耗时占比达45%,而达索系统3DEXPERIENCE平台支持多部门协同仿真,使造型设计与工程验证同步推进。保时捷应用该平台后,整车开发周期从60个月压缩至36个月,工程变更次数减少80%。这种流程再造产生的效益已超越技术本身,形成组织层面的创新动能。
云端仿真生态加速了技术民主化进程。AWS与ANSYS合作的云仿真解决方案,使中小企业可用1/10成本获得超级计算资源。某医疗器械公司通过云端仿真集群,将CT机架结构验证时间从2周缩短至8小时,研发投入产出比提升5倍。这种资源获取方式的变革,正在打破大型企业的技术垄断格局。
四、经济价值转化
成本结构发生根本性改变。施耐德电气在低压电器开发中,通过仿真替代85%的物理测试,单产品开发成本降低40%,质量投诉率下降60%。更关键的是,虚拟验证产生的数据资产形成新的价值增长点,西门子数字孪生平台每年为客户创造12亿美元附加价值,证明仿真技术已从成本中心转化为利润中心。
商业模式创新催生服务化转型。PTC的Vuforia Expert Capture技术,将专家经验转化为可复用的仿真模板,使某重工企业设备故障诊断效率提升90%。这种知识封装模式推动技术服务从项目制转向订阅制,ANSYS 2022年云服务收入增长67%,占总营收比重突破30%,标志着行业进入服务化转型新阶段。
(总结部分)
数字化浪潮下的产品验证体系,正在经历从物理世界向数字空间的战略转移。仿真软件不仅将验证效率提升至新高度,更创造了"测试即设计"的新型研发范式。当宝马集团用数字孪生技术实现整车生命周期管理,当SpaceX通过仿真完成火箭回收系统的80%验证,这些实践揭示着制造业的未来图景。面向工业4.0时代,仿真技术与物联网、区块链的融合将催生更智能的验证体系,而量子计算的应用可能将仿真速度再提升数个量级。这场验证革命的下个里程碑,或许将是完全虚拟化的产品认证体系,这需要产学研各方在标准建设、算法优化、硬件协同等领域持续突破。