高效智能驱动工厂管理系统软件革新升级
19429202025-03-21WIN软件13 浏览
一、工厂数字化转型,花大钱真的能解决效率问题吗?
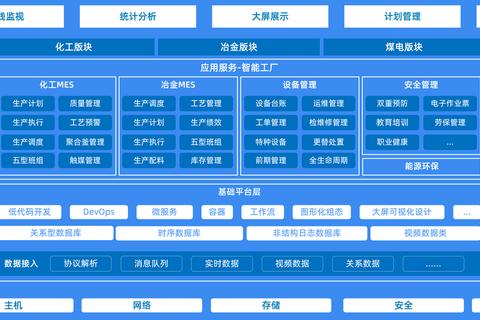
某铸造厂老板曾向笔者抱怨:“去年花300万上了套‘智能系统’,结果库存误差率反而从5%升到8%。”这并非个例,第三方调研显示,2024年制造业软件系统实施失败率高达67%。传统ERP系统部署周期动辄18个月,等系统上线时市场环境早已天翻地覆。这场数字化转型的困局,正将高效智能驱动工厂管理系统软件革新升级推上风口浪尖——究竟怎样的系统升级,才能让工厂真正实现降本增效?
二、智能排产:算法能否破解“计划赶不上变化”魔咒?
广东某半导体企业曾面临订单准时交付率不足60%的困境。引入格创东智的CIM系统后,通过AI算法将设备、物料、工艺参数等200+变量纳入排产模型,动态调整速度从小时级缩短至分钟级。数据显示,其排产效率提升40%,订单交付周期压缩28%。这套系统的核心在于:
1. 多源数据融合:整合ERP的订单数据、MES的工序进度、SCADA的设备状态,构建实时数据湖
2. 动态优化引擎:当某台光刻机突发故障,系统能在30秒内重新规划替代工艺路线
3. 人机协同决策:车间主任的排产经验被转化为决策树模型,与算法结果交叉验证
三、透明工厂:如何让车间管理告别“黑箱操作”?
浙江某汽配厂曾因质量追溯不力,单次召回损失超500万元。部署黑湖科技的可视化控制塔后,通过三大改造实现管理透明化:
设备互联:在200台CNC机床加装智能传感器,振动数据异常自动触发保养预警
工序追溯:每个零件的加工参数、操作员工号、质检记录形成区块链档案
实时看板:厂长在手机端可查看任意工序的实时OEE(设备综合效率)
实施半年后,该厂质量追溯时间从3天缩短至10分钟,设备非计划停机减少62%。这种透明化管理,正是高效智能驱动工厂管理系统软件革新升级的典型应用。
四、数据驱动:沉睡的TB级数据如何变成真金白银?
山东某纺织企业的案例极具启发性:其MES系统积累了5年生产数据却从未利用。引入道一云数据工厂后,工程师通过低代码工具构建了三大分析模型:
1. 能耗优化模型:发现染色车间蒸汽管网存在12%的热能损耗,年节省成本80万元
2. 工艺参数优化:通过机器学习找到最佳染液配比,染料用量降低15%
3. 设备寿命预测:基于振动频谱分析,提前2周预判梳棉机轴承故障
这套系统让该企业数据利用率从不足5%提升至68%,年综合收益增加1200万元。
给工厂管理者的三条实操建议:
1. 分步实施策略:优先解决订单交付延迟、质量追溯困难等核心痛点,避免“大而全”的系统陷阱
2. 选择可扩展架构:确保系统支持工业物联网设备接入,预留与ERP、PLM等系统的标准接口
3. 重视数据治理:建立从数据采集、清洗到分析的全流程规范,培养既懂工艺又懂数据的复合型人才
这场由高效智能驱动工厂管理系统软件革新升级引发的制造业革命,本质上是用数字技术重构生产关系的进程。当算法开始调度设备,当数据流比物料流更关键,那些率先完成数字化转型的工厂,正在书写智能制造时代的新生存法则。